|
 |
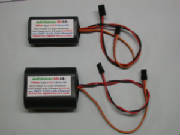
|
Click Here to Order A123 Packs & Equip |
|
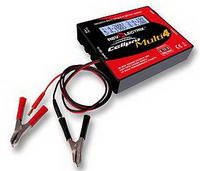
|
Click to Go to Chargers & Accessories |
|
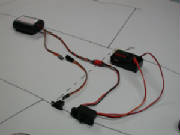
|
Click Here for the A123 Setup Guide |
|
Thinking about Migrating to A123's? Here's the Definitive A123 Overview and FAQ for Giant
Scale -
Here at NoBS the A123 LiFe battery system has been a major part
of our product lineup since 2005. It's since been deployed into commercial transportation operations and tooling applications
and the technology continues it's natural migration into the hands of modelers all across the hobby.. Electric Flight,
RC Cars, and my particular area of interest and expertise.. Commercial/Military RPV’s, Giant Scale RC & Warbirds
and 3D IMAC type applications. If your looking for application info and assistance with the pressing questions of what motor
pack, controller options and props would work best for your buggy or your electric powered airplanes.. move along. Nothing
for you here. For you folks that are looking at this technology to replace the NiCad and NiMH Rx, Ignition, Servo
and ECU packs in your big birds.. you are in the right place. I’ll try and hit the high points
first, then move into general application and use notes as we progress with this. As with the NiCad and NiMH FAQ I’ve
put up on this site, it’ll be a work in progress. * NOTE:Be sure and vist
our A123 Setup Guide for application information on connectors, chargers and aircraft set up. * First.. what is A123? Well, simply put; this is the iteration
of Lithium Technology that won’t burn your shop, plane or house down if you do everything right. Or wrong. In the ‘industry’,
these cells are referred to as LiFe PO4 cells.. also called ‘nanophosphate’ or Lithium-Iron… confused yet?
Yah; me too. For the sake of sanity and ease of labeling I’ll be calling them what the MFG/Importer calls them.. A123
LiFe, type M2. * Ok, now that we’ve identified what we’re talking about,
let’s look at what they can do for us Giants and Big 3D fliers... Again, for ease of digestibility, I’ll compare
them in broad terms to the technologies we’re flying now and try and keep the relationships on a level we can all relate
to without finger paintings. * Q: How do these compare to the Sub-C
NiCad’s I’ve been using for the last 4 or so decades? * Ok, this one will need some breakdown.. first; size and weight. Dimensionally, the cell is FULL C in diameter, and
about half again as tall as a Full C cell.. and that’s bigger than Sub-C Nicads like the 2400 Sanyo. On the other hand,
they’re verylight.. and only two cells are required to build up an Rx or Ignition pack. Next, weight savings
on the plane usually amounts to half the weight of a sub-c NiCad and about the same rated capacity. Pay attention to that
rated capacity bit.. I’ll get into that a bit later. * Q:
Are they as dependable as NiCads? * A dependability
comparison against NiCad’s has been the Achilles Heel of Lithium technologies… until now. Folks, these cells
astonish me.. and this is the first cell I’ve ever seen that will actually outlast in calendar life AND duty cycles
the venerable Sub-C NiCads. * Right along with dependability also rides the
pressing question of our use of these cells in Giants and 3D birds.. the performance under load. Here, they again out perform
NiCad’s. Yes, they are stable. Yes, they are capable of handling far more current that we will ever be able to
load them with in a Servo/Rx environment on ANY size 3D bird. Here, the typical off the shelf R/C wiring, connectors and switches
tend to lag significantly behind the newest demand loading capabilities of today’s massive high torque, heavy duty
digital servos used at the 33-45% level… Obviously, focus still needs to be applied to the power handling capabilities
of modern 3D radio gear in the REALLY big birds.. Finding 22g cabling and tiny industry standard servo connectors on a 200in
oz digital servos is laughable. But, that’s what they sell… improved switches and power sharing boards from outfits
like SmartFly and Duralite are leading the way and at this writing the new 9100 Series JR power share receivers show promise..
but the point is, power handling and impedance with the LiFe M1 cells is just not an issue. * Q: What about NiMH.. I use the big Sub-C NiMH packs, they have lots more capacity than the A123 packs.. * Ok, here’s where we get to compare some definitions of ‘rated capacity’ vs ‘usable capacity’.
Again, without getting into numbing graphs and finger painting, the short explanation is that we get to use a LOT more of
the A123’s rated capacity when compared to NiMH or NiCad. Why? Hugely low internal impedance as the pack discharges..
a marked difference in these vs NiMH or NiCad.. as the pack discharges the impedance does not increase.
This means we can use a significantly larger portion of the rated capacity without worrying about those low voltage spikes
kicking our Rx’s into failsafe or reset. * Next.. Lets look
at the emerging Achilles Heel of NiMH for a moment.. longevity and self-discharge. This has been a rats nest of problems..
folks used to NiCads are routinely disappointed by the short cycle and calendar lifespan of NiMH vs NiCad, let alone the self
discharge issues. Getting more than a season or two out of them is problematic, if the bird is flown infrequently there’s
often issues with dead cells from overdischarge. And for folks running them, the A123M1 is a godsend. There is NO significant
self-discharge issue. Charge retention across 9 months in the tests we ran here was 94%. Simply amazing. We’ve not been
able to determine yet what the serviceable calendar lifespan is.. duty cycle lifetimes in the electric flight world at insanely
high current loads indicate capacity loss is detectable.. but cell serviceability and impedance remains unaffected.
In a Giant Scale or 3D 40% application.. I just don’t know what the lifespan limit is yet; but I do know they’ll
outlast any NiCAD, NiMH or LiPoly/LiIon pack. * Q:
How do they compare to Li-Ion and Li-Poly Rx Packs??.. I’ve been using those with pretty good results so far in my big 3D birds. * Aren’t you the lucky one! And, as far as
LiPoly goes, I’m convinced that luck has a lot to do with satisfaction and success. At least more of it than I’ve
got. The biggest gripe I have against LiPoly is the flame up issue.. closely followed by the dependability issue. The wafer
thin plates and cell straps, fragility, vulnerability to vibration alone are enough to keep me away.. add in the need for
a regulator and you’ve lost my interest entirely. With LiIon.. high impedance and short longevity and the need for that
pesky voltage regulator also keeps them off my table and out of my planes. With Li-Ion, the only way to keep the impedance
at a workable level was parallel systems. The weight build up, complexity and short lifesapn (plus the regulators again)
leave a lot to be desired. Now we've got something better! - Which finally brings us to why I like this cell so much in Giant Scale
and IMAC 3D.. it’s robust ability to handle loads, it’s refusal to flame up even when abused, it’s light
weight, it’s over-all longevity, it’s seamless transition into aircraft already equipped with conventional LiIon/liPoly
or Nicad/NiMH systems. For the LiIon LiPoly guys.. you get to ‘lose’ the regulators, cut the costs in half and
at least double or triple the longevity… and get a more dependable system. For the NiCad/NiMH guys, you’ll need
a quality charger that can handle A123 (LiFe) balance charging and a quick mod to your existing chargeport switches..
that’s it. The cost of the charger (about 70 bucks) is offset in the second year.. by not having to replace the
packs. * Q: What's the difference between A123 LiFe packs and LiFe PO4 packs like Hobbico's LiFeSource™ packs? * Two big differences. First, A123's patented 'Nano'
plating technology.. at a molecular level the negative plate material stands like a shag carpet rather than laying 'end-to-end'.
This produces an incredible amount of surface area gain for A123's negative plate and it's why A123 can tolerate immense current
loading without voltage sag. Another benefit to the nano plating technology is a huge increase in cell life. All stored energy
systems consume negative plate over time.. with 100+ times the negative plate surface area generated by any competitors
plating process the lifespan of the A123 cell is extended immensely. Next, A123's are aluminum cased cylindrical
cells with welded alloy end plates and towers like a Nicad cell. This enables a rugged welded strap pack assembly
system (like Nicads) that is exceptionally robust and very resistant to vibration and hard knocks. The LiFeSource™
packs are built with wafer stacked 'bag' prismatic cells.. like LiPoly. And, like LiPoly, they are fragile, the cell
link tabs are very thin alloy strips and the entire assembly is as a result susceptible to rough handling and vibration.
Further, the prismatic cells and their tabbing system are unable to handle anywhere near the current loading the
A123 system can tolerate with ease. * Q: Ok, so, where’s the Achilles Heel with LiFe? * Mostly in mindset and field habits of folks used to NiCads and NiMH.. there's new things to learn & some folks
don't like things moved in their cage. On the 'technical' side, there are several 'issues' that routinely crop up, in
no particular order they are: - 1.
Non Balancing 'smart chargers' and the myth that A123's 'don't need balancing'. A close to fully charged pack, deeply discharged pack or out of balance pack may be easily mis-identified
by a 'smart' charger WITH THE WRONG CELL COUNT. The results are usually always a ruined pack. If a quality balancing
charger is used and correctly connected, the charger will see the individual cell voltages in the pack, correctly identify
it's cell count and usually report on the individual cell voltages all the way through the charge routine. If 'smart' means
stabbing a button and waiting for a green light... well; that might not be an appropriate charger for a critical application
battery pack. - 2. Attention to the Details. As a general rule, success in flying
Giants more often than not relates directly to the operators attention to detail and getting a firm grip on what is likely
to be a new knowledge base (as is usually the case when switching your battery type to A123's). Getting
the charger and pack wiring configured correctly, charge program selection and close attention to little things like
cell balance, switches being left on and over-discharging the packs all impact success with the system. The reality of being routinely
distracted at the field and at events can impact our ability to focus clearly on the tasks at hand. In order to repeatedly
and routinely safely commit a Giant Scale Aircraft to controlled flight means that the operator has to know their
limitations and the limitations of their equipment, and institute routine pre & post flight checks and procedures consistently,
regardless of the pack technology he chooses; as the pilots mastery of the details are crucial to us all
in this sport and most certainly no less so when flying Giant Scale. - 3. Connector
Gripes. Plugging the three wire charge cord into the switch chargeport or universal cell tap backwards (upside
down) will usually result in the charger 'seeing' just one cell.. the results are an out of balance pack. The cure is to use
the chargers 'balance charge' or 'accurate charge' routine ALWAYS... and then YOU check the display to be sure the charger
has correctly identified the cell count -. 4. Compatibility with Smart Chargers that ain't
all that smart. I actually had a R/C dedicated charger mfg tell me I had to stop putting R/C standard plugs
for balance charging on my 2 cell Rx packs. His customers were plugging the R/C standard (JR/Univ) plugs into their supplied
balancer board which apparently cooks the balancer circuit. I asked him why their charger doesn't provide the ability to interface
with every R/C standard switch chargeport commonly in use.. or provide an adapter? Or, in case the guy plugs it
in wrong... not cook itself? - I do see his point... JST-XH is the 'standard' goofly little white molex plug used or supported
by 90% of balancing chargers and packs available in the hobby. Unfortunately, in this thin slice of the hobby (the one
I build for) checking and charging individual cells in a 2 cell A123Rx pack while in the plane is a requisite
for safe operation of 30-50 pound aircraft. That's not open for debate OR compromise.. it's just a fact. And,
last I checked; molex connectors are not compatible with R/C system standard chargeport switches. And that's why I'll
continue to supply my packs to my giant scale customers with the R/C standard Univ connector (FJ/JR/Hitec/AirtZ) balancing
plug.. which covers just about 100% of my customers chargeport switches. * Q:
I have an A123 pack that's 2 years old from another supplier and when I was charging it yesterday (Turnigy accucell 6) the charger alarm went off and it
said “broken connection”. The battery was really hot. Obviously a short somewhere. I stripped
the shrink wrap off of it to see if one of the connections had come loose. Nothing apparent on the outside, so my conclusion
was that it fried on the inside. I get a .14 volt reading from my meter. Any idea what may have gone wrong with the
pack? Since I only use A123s and only use the Turnigy Accucell 6 on all my planes, I need to know if I’m doing
something wrong.
* Yup.. sounds like a short
failure on one of your cells in that pack. Uncommon but not unusual.. biggest root cause we found so far
relates to 1st, (most common) a 'run-flat' (severe overdischarge) at some point in the packs history, an incorrect
charger sub-routine, such as accidentally triggering a liIon, LiPoly, Nicad/NiMH charge setting at some point in the packs
history and/or routinely using a non-balanced charge setting. Repeated non-balanced charging will set up a severe imbalance,
results are one cell hugely over voltage on charge and that cell eventually shorting. - 2ndmost common root cause of cell shorts and breakdowns is pack installation… the prime enemy of all
stored energy systems is heat and vibration. Seems like a lot of folks ‘graduate’ to Giant Scale from smaller
electrics and they never learned the Engine Powered Flight equipment setup basics.. pad the pack and radio gear, isolate them
from vibration sources as much as possible and keep them away from heat sources. Despite this very basic install principal
learned over decades of fuel powered R/C & RPV darwinisim I still see ‘naked’ packs and Rx's wire-tied, velcroed
or strapped to firewalls, formers and cross members. Not good. The constant low frequency
vibration imparted by the engine to the airframe breaks down the internal structure of the cell and creates chafe-wear shorts
between plates and insulators and in extreme cases, shears welded straps.. Better to fully wrap the pack in a layer of dense
foam with tape, then ‘soft’ velcro that package to a padded cross member some distance from the engine (NOT a
firewall), and kept well away from heat sources. * The Reply: Great help!! Thanks!
I understand
about padding the batteries. I grew up in the age of 40-60 size glow engines and learned early on that receivers and
battery packs don’t last long in a harsh vibration environment. I think it is entirely possible that the charger
routine could be the issue. I once left the switch on and ran the battery completely down. My charger wouldn’t
recognize the battery because the voltage was too low. Your competitor told me to put it on a NiCd routine for 6-7 minutes
to get the voltage up and then switch it over to the LiFe routine. I did and the battery came back up. I used
it happily thinking that I had saved the pack. I’m also not the best at using the balancing plug. I have
a tendency to charge it and fly it. Won’t do that again unless I’m at the field and putting in an extraordinary
number of flights. * A: “Your competitor told me to put it on a
NiCd routine for 6-7 minutes to get the voltage up and then switch it over to the LiFe routine.”- That didn’t do any damage.. it’s allowing the cells to climb above terminal voltage further
along in that charge process that would damage it. A soft ‘run flat’ would set the problem
up tho; this situation can cause one of the cells to be slightly degraded (impedance and capacity is affected) and from that
point on, keeping the pack balanced is very problematic if you don’t routinely balance charge. The Key Issue in your
case is revealed in your reply.. not checking individual cell balance every time you charge and before you fly.. THAT is how
you stay outta trouble and it’s why we put a JR/Univ balance plug on the A123 packs.. so with a simple adapter you CAN
easily check the pack and it’s cells via a simple R/C standard chargeport while the pack is in the plane. * Q: Can
I use a Load Tester to check my A123 packs relative state of charge? * Here's an area where A123's are radically different than
Nicad or NiMH packs... Load Testing A123's in the traditional way is ineffective for determining state of
charge... the beasties just don’t 'react' like we expect.. a 1 amp load for 10 seconds will convince somebody not
familiar with them that there’s something wrong with the load tester or the pack.. the needle starts to sag after a
few seconds with some meters, (resistor impedance values jump up rapidly under the continuous load) and decreasing
voltage displayed on the meter usually indicates approaching doom for the resistors, switch & connectors rather than reflecting
any useful info on the state of charge for the pack. Continued loading can melt out connectors, meter resistors, switches,
etc. ESV 'loading' just doesn't work with A123's in the tried and true sense as the cells are quite happy delivering
enough amperage to melt out your gear, even when nearly discharged. Because of the incredibly flat discharge curve and
the ability of the cell to deliver massive amounts of current, using a standing voltage level under load to decide when to
recharge can lead to a disaster via damage to switches & connectors... Further, when A123's DO go flat, they do so remarkably
fast. So, we go to the next question.. * Q:
How do I know when to recharge? * This one still
gets me smiling.. old codgers like me already know the answer.. the same way we did it before some bright boy came up with
the hobby ESV. We fully charge the pack, cycle it to determine capacity. We recharge, fly three or 4 flights, keeping track
of the time and the voltage on the pack under the 1 amp load after each flight. At the end of the sessions, we'd discharge
the pack to determine capacity remaining and do a bit of math.. we divide the time by the total capacity used and determine
how much air time we can safely expect to get out of the pack.. and then cut that in half. Thankfully, most quality
A123 capable chargers have a MAH charge counter.. it records the amount of energy it puts in the pack so we don't have to
resort to the 'antique' methods of yesteryear.. just charge before you fly and charge again after you fly... the amount of
energy used in the flight will be right there on the charger's screen. - Some specifics.. the M1 cell rates average 22-2300ma.
Voltage drop cliff starts at about 2,000ma. I don’t like to get lower than about 50% remaining before recharging. (I’m
a very conservative old codger) My bird used 800ma from the pack in four 10 minute flights (big warbird). I figure I got 5
flights to 50%.. so I field charge on the end of the 4thflight. Yes, I still use the load tester.. and yes, old
habits die hard, and checking the voltage between flights is still how I recommend you stay outta surprise territory…
but a Load Tester alone is not enough to keep you out of trouble. There are however ways of improving your odds... and this
one's important: These are NOT NiMH or Nicad packs. The act of balance charging them at 1C just does not stress
the cells a bit. So, if in doubt, CHARGE! Use a quality balancing charger, and get in the habit of checking
individual cell voltages. Since virtually all of the quality A123 capable chargers have a MAH counter that records the amount
of charge transferred to the pack, before very long, you'll get a good feel for what's 'going on' with your new technology
packs in your bird and your confidence in yourself, your power system and your charger will benefit greatly. - Recommendation: FMA's Multi4 and CellPro chargers can help keep track
of relative charge state (the charger has a very conservative 'fuel gauge' feature as well as MAH transfer recording and displays
individual cell voltages) and VoltMagic can keep track of Peak Low Voltage on board the aircraft.. Below is the discharge
graph from VoltMagic on comparative technologies.. this inexpensive device is a godsend for A123 users.
Click here to read more about VoltMagic. -
VoltMagic PLV Trigger Points, Various Pack Types |
|
click picture for more detail |
Q:
How does Nicad or NiMH usable pack capacity compare to A123's? Same flight time for the same capacity? - The example
plane here is a 1/4 scale warbird equipped originally with a single Sanyo 2400ma 5 cell NiCad pack. Load testing between flights,
I’d get 4 flights before the ESV at 1 amp would display under 6v, indicating ‘recharge’ time. Cycling the
pack at that point revealed the same amount of ma consumed on average… but that was it for flying the pack. In essence,
the NiCad gives up a bit more than half it’s rated capacity before I got to a required recharge point.. the LiFe would
go much further.. if it had to. The Nicad wouldn’t. Net effect is seamless to me though.. either way, I was
recharging after 4 flights… but carrying significantly more ‘reserve’ usable capacity with the LiFe
pack. It must also be mentioned that both Nicad and NiMH INCREASE impedance as they discharge.. the LiFe pack did not..
another significant bonus. * Q:
Can I use my ‘XYZ’ brand NiCad /NiMH charger or Wall Wart on LiFe? * No. Let me be specific… HELL NO! Here’s what’s going on.. LiFe’s nominal
voltage per cell is 3.3v. While the charge routine is similar to LiIon or LiPoly, the max allowable voltage under charge is
lower than any other Lithium technology cell, usually about 3.6v; so using a standard LiIon or LiPoly charger will do damage.
For you NiCad - NiMH guys, the entire charge sub-routine is different . As of now, there are a number of LiFe capable
superchargers coming into the marketplace.. these will deal with ‘em as well as the various other types of Lithium and
NiCad/NiMH packs but assume my first answer of HELL NO applies until you review your chargers manual. If you not sure, contact
the charger mfg or distributor. Don’t let ‘em blow smoke up your backside either. Get it in writing if it’s
not called out in the manual. * Q: What in heck
is the 'Cell Balancer' function all about? * Simply put, this monitors voltage of the individual
cells and keeps them closely matched or ‘balanced’ in voltage during the charge routine.. Some A123 enthusiasts
(and charger MFG's) will try and convince you that A123 packs don’t 'require' balancing. This claim is
bunk for those of us that value what we fly... Unbalanced charging may be adequate for a tool pack or a ground application,
however the reality of field trials with a wide variety of non-balancing LiFe capable chargers has demonstrated that balance
charging is the best way to avoid damage to the pack and reduce risk for the aircraft. Balancing= Good for the pack,
good for the plane. See the A123 Setup Guide for how to easily accommodate balance charging at the field. * Q: My A123 pack has 2 connectors.. which do I charge thru? * In
the most common A123 pack wiring configuration there are two leads. The 3 lead wire and connector is the 'cell tap' or
'node' connection.. The heavy gauge 2 wire lead wire is the standard pack 'feed' that connects to the switch harness.
Don't attempt to hook the 'cell tap' lead to anything BUT the node or celltap port of a balancing charger via an appropriate
adapter for your charger's balancing port. While the pin spacing on the JR/Univ celltap connector we install on our packs
will fit in some 'balancer boards' it likely does NOT have the correct pin polarity for your charger's balancer. You'll
need an appropriate adapter to 'translate' the JR/Univ celltap to your charger's pin convention. This 'balance'connection
is used by balancing chargers that require a separate three wire connection to the charger in addition to the two wire pack
feed to accomplish a balance charge. If you are not balance charging, or are charging at high rates, charging should
be done on the standard pack feeds as with NiCad and NiMH packs. *
Q: I've seen some NoBS A123
packs that have just one ONE heavy three wire connector and no separate two wire power feed. How come? * That's the 'Combo 3 Wire 20g Feed' option. This cabling &
connector setup allows quick and easy access to the pack via a standard chargeport switch without need for a second separate
chargeport dedicated to just balancing and cell voltage checks.To make use of this, a simple mod has to be performed on most
switches... the 'third' lead or 'signal' wire that runs from the switch to the Rx has to be removed to enable the feature. We've
got pics and a description with complete instructions on how to take advantage of this on our A123 Setup Guide. * Q: Why do you have a JR/Univ celltap on your packs instead of either a JST-XH
or FMA molex plug? * A: We've learned that the key to safe and trouble free
operation of ANY Rx pack (including A123 two cell Rx packs) is dependent on the pilot being able to readily access the
pack to check it while inthe plane before flight. This is even more critical
with A123 packs, cell voltages and balance condition are crucial to the 'fly-no fly' decision. If the aircraft has to
be 'broken down' to gain access to this basic flight safety check.. then the pack will not get checked before flight. Sadly,
not one of those goofy little molex plugs (FMA, JST-XH, etc) will mate with an R/C Standard HD chargeport switch. Since the
chargeports on these switches are how we all have for the past 2 and a half decades gained access the pack in the plane to
check it, that's the connector we put on the pack. ... so you CAN easily check our A123 packs and charge individual
cells or balance charge the pack easily. You'll need an adapter to mate your chargers balance port
with the JR/Univ standard switch chargeport. You can either make one of your own or purchase one pre-made to fit your charger's
balance board, they are available on the A123 packs page. * Q:
I have an FMA Charger .. it charges ONLY through a 'node connector'.. do you have an adapter for your 'standard univ'
cell tap? * Yep.. See the question above & check the notes
below on how to make an extension from the univ celltap or charge switch port to any brand chargers balance port. * Q:
I need to make an adapter cable for my 'Brand X' balancing charger for your 'Univ' cell tap. What are the color codes
on your univ tap plug? * The 22g univ tap connector on
our two cell packs is very easy to build an adapter for. Using an aileron extension to make an extension/adapter cord is a
snap for any charger.. Just snip off the 'male' servo end from the aileron extension and solder a 'pack side' plug that mates
with your chargers balance port.. red is pack positive, black (or brown) is pack negative and the white (or yellow) lead is
'node 1' on your balance plug. Another way to explain what that white or yellow lead is relative to the red and black.. it's
the 'negative' for the red lead, or the 'positive' for the black lead, allowing the charger to 'see' the individual cell voltage
during the charge. * Q: Do I need to ‘balance’ the pack every charge? * The only
way to avoid costly and aggravating fried battery packs is by using a balance charger EVERY TIME.. Here's the prime issue:
A close to fully charged pack, deeply discharged pack or out of balance pack may be easily mis-identified by a 'smart' charger
WITH THE WRONG CELL COUNT. The results are usually always a ruined pack. If a quality balancing charger
is used and correctly connected, the charger will see the individual cell voltages in the pack, correctly identify it's cell
count and usually report on the individual cell voltages all the way through the charge routine. Virtually every pack failure
I've seen to date relates back to a 'smart' charger incorrectly identifying the cell count or state of charge of the pack..
with a wiped out pack (at the minimum) being the end result. I Use the FMA Multi-4 and like it's ability to balance charge
with just a single 3 wire connection between the pack and the charger.. it reports on individual cell voltages, provides a
conservative 'percent of charge' report on the pack at the start of the charge and reports on individual cell voltages at
the end of the charge. This is utterly crucial with A123... to stay out of trouble, knowing and
observing individual cell voltages at the start and end of the charge is the only SURE way to determine relative charge state
and condition for the pack. * Q:
What changes do I need to make to charge these in the plane? I’m using HD JR switches.. do I need new ones? * Nope.. no new switches required although you will likely need to 'mod' the output lead from your switch to the Rx from
three wires to two. (see question below this one) Two approaches to use here depending on the type of charger you are
using. Most balancing chargers use two connections to the pack; a three wire 'balance tap' lead as well as the power
feed. Some balance chargers, like FMA's Multi-4, will balance charge with just one connection to the charger. EyebalI the
Setup Guide to determine how to take advantage of the simpler 'single 3 wire combo' set up if you have an FMA charger.
If your charger requires the dual connection setup, you'll order the pack with a separate balance tap and separate power feed.
Since virtually every ‘balancer’ equipped charger out there uses a different oddball plug to connect the balance
tap to the charger I standardized the packs tap to the industry standard universal servo connector for the balance tap lead.
To connect to the universal balance tap on the pack all you need is an aileron extension with the plug that fits your
charger balance port spliced onto the other end. Now, if you balance charge during setup before the first flight of the
day, no extra stuff need be added to the plane.. hook the chargers accessory balance lead to the pack tap. The ‘bonus’
part with the ‘standardized’ tap on the pack pops up when you decide to balance charge in the plane with your
two-connection charger.. all you need is a ‘ernst’ type chargeport in some convenient spot on the plane and a
standard aileron extension from that to the battery balance tap connector... and then you can use the same cable you used
to connect directly to the packs tap to plug into the 'ernst' chargeport to connect to the charger. I like simple. A
LOT. * Q:
My A123 packs are just a few months old and now they won't balance.. Cell #1 is lower than Cell #2 and my balancing
charger won't re-balance the packs. Is there something wrong with my Packs? * A: In this
case, there was a 'set-up' error with the switch or the charge cord. Most often, when I find just cell #1 way under voltage,
a check of the switch reveals the cause.. the plug going to the Rx has three wires.
Folks, if you plug a three wire lead from an A123 pack into a
switch with three wire inputs and three wire outputs, the switch will pass the connection
of that 'third' lead out of the switch and into the three wire cable going into the
Rx, Smart Fly Power Expander, Ignition Module or any other aftermarket device the switch output is plugged in to..
That third lead IS HOT!.. and this unwanted connection of the cell tap PAST
the switch will drain cell #1, knocking the pack drastically out of balance. In some cases it can also mess with the
Rx, causing unstable operation. If the cell is run flat, you may damage that cell. If the voltage spread between the cells
gets large enough, the charger will likely NOT be able to re-balance the pack. To correct the voltage spread, you'll need
to charge cell #1 independently of cell #2 to get them close in voltage, then you can re-balance the pack with the balance
charger in the usual way. To keep this from happening again, make sure you remove the third wire from
the plug on the Rx (or output) side of your switch! See the notes in the question above and refer to the
Setup Guide for 'Switch Mods' (towards the bottom of that page!) on how to easily mod the switch's output lead from
3 wires at the Rx plug to two to avoid this issue. * Q:
I've got the same situation as above... but my switches are 'modded' and I have an FMA Multi-4 and I'm charging thru the switch
chargeport. Why is cell #1 three to four tenths of a volt lower than cell #2? * A: If this
is a 'one-time' or occasional issue then you've likely been occasionally reversing the charge cord plug.. plugging
it in 'upside down'. When that happens, the charger will only 'see' cell #2 and come to the conclusion that it is being asked
to charge a single cell (1S) pack. You don't get a reverse polarity charge... you just get no charge
to cell #1. How to avoid this? Your CellPro or Multi-4 has several 'mode' screens when the charger starts.. the various screens
display a ton of info.. including pack cell count and individual cell voltages. CHECK IT! Every
time. I use the 'accurate' charge routine and as soon as the charger accepts the charge command after verifying
with me that it is an A123 pack, I scroll the screens using the 'mode' button to confirm cell count and cell voltages. If
you see '1S' displayed and only one cell's voltage is reported, you are plugged in upside down. Just unplug, invert the plug,
plug back in and restart the charge. When you are plugged in correctly, you will see '2S' and two sets of voltage data
when you get to the cell data screen, one for each individual cell in your two cell Rx pack. Regardless of what
type of charger you use, with A123 packs being charged through charge ports with Univ three wire connectors, it would be a
very good idea to mark your charge port for correct charge plug orientation. Remember, This
is utterly crucial with A123... to stay out of trouble, knowing and observing INDIVIDUAL cell voltages at the start and end
of the charge is the only SURE way to determine relative charge state and condition for the pack. If
the out-of-balance condition returns routinely after re-balancing, then you may be seeing the manifestation of damage to one
of the cells in the pack.. review the 'won't hold balance' question a bit further down in this FAQ. * Q:
I've done the switch modification per your Setup Guide.. works great, but I'm curious as to how that will affect the binding procedure. Can I still 'bind' my Rx via the
switch chargeport? * Nope. Most all HD chargeport switches are set up with three wire feeds to the RX, the original
intent was to enable the 'DSC' feature available on top end 72 MHz Tx's. 'DSC means 'direct servo connection'.. it gave
you a means to power up and actuate the Rx and servos on the plane without actually 'transmitting'. Early on, this switch
feature also enabled 're-binding' via the switch chargeport on some 1st generation 2.4 systems that would lose 'bind' fairly
often. In a world filling rapidly with second and third generation 2.4 GHz radio systems the DSC feature is not often required
for binding and 2.4GHz Rx ‘re-binding’ in the plane is not common. If you find yourself needing to 're-bind'
with the Rx in the plane, it can be quickly accomplised with an aileron extension plugged directly into the Rx's 'Batt/Data'
port and moving the two wire feed from the switch to an 'Aux' port on the Rx to power the Rx during the process. Note
that currently all initial 2.4 radio binding is normally done on the bench before the Rx is installed and that current
versions of 2.4 radio gear rarely requires re-binding at the field. If you do find yourself needing to bind or re-bind,
you won't be able to do it via a modified switch's chargeport; you must use an aileron extension plugged directly into the
Rx. * Q: My packs
occasionally get far enough out of balance that my balancing charger doesn’t bring up the low cell in a reasonable amount
of time. Why? Seems to take forever! * Here’s a good chance to discuss briefly cell balance or
‘equalization’. One of the striking differences between a 5 cell Nicad or Nimh Rx pack and a 2 cell A123 Rx pack
is the relative effect ‘balance’ between the cells has on the security of the flight system . When the relative
state of charge in the cells of a 5 cell Nicad or NiMH pack get out of balance, or in other words, the pack is not ‘equalized’,
the impact of the one or two slightly ‘out of balance’ cells to the system is minimal when the pack is in the
upper half of it’s discharge curve. While the overall capacity of the system is reduced to the capacity of the lowest
cell, since we normally don’t get very deep into the lower half of the pack’s discharge curve during normal use
‘cell balance’ rarely crops up as an issue. Next, because Nicads and NiMH systems use ‘constant current’
charge algorithms, the process of slow charging or ‘topping off' after a peak charge does the ‘re-equalization’
for you as part the normal charge process and small differences in cell capacity and impedance between the cells are massaged
right out of the picture as a result. * Since Lithium types (A123 is a lithium based system) require terminal voltage control as the charge
algorithm and ‘going overvoltage’ kills Lithium cells outright, the charger terminates the rapid charge as soon
as the first cell in the pack hits the voltage ‘roof’. The end eventual result with unbalanced charge routines
on A123 packs is that normal variances between cells in capacity and impedance are not ‘massaged’ out of the picture.
The net result is that over a relatively short number of unbalanced charge-use-recharge routines the imbalance condition can
get very pronounced. If the imbalance is large enough when a ‘balanced’ charge routine is finally used on a seriously
out of balance pack most chargers will kick into a very low charge rate at the point the charger senses the high voltage cell
is near full charge, either cutting charge off to the near fully charged cell and/or sending a paltry 100ma ‘balance’
charge to the ‘low voltage’ cell in the pack. And if your packs low voltage cell is only half way to full charge
when the other cell gets to ‘full voltage’, then that’s why you may be staring at that charger for quite
awhile (sometimes many hours) waiting for it to get the pack back in ‘balance’. * Now, here’s the crucial issue with flying an un-equalized or unbalanced
two cell lithium pack…If the ‘lower voltage cell’ has only 800ma of capacity remaining and the higher voltage
cell has 2000ma... you have a 800ma capacity pack. Now, here’s the bit of info that will make you squirm in your chair…
only three TENTHS of a volt separates a fully charged A123 cell from a dead one. This is why it’s crucial to have BOTH
cells at or near full capacity when you start using the pack, why it’s crucial to monitor and check individual cell
voltages and why you should routinely employ your chargers balance charge feature (if it has one) or equalize the pack routinely
rather than occasionally… it not only keeps the pack’s cell voltages ‘in range’ of the packs ‘balancer’
feature, it gives you the benefit of the full range of capacity of the pack. An un-equalized or ‘out of balance’
2 cell lithium pack is not conducive to that ‘warm and fuzzy feeling’ we’re all looking for from our Rx
power system, folks. * Q: Ok, I get why it’s important to keep the cells close
to each other in voltage but I’m a bit fuzzy on the difference between ‘balancing’ and ‘equalizing’. * A: Nothing other than how it’s accomplished.. ‘balancing’ is what the charger
tries to do when you put it in a balanced mode charge routine (FMA calls this ‘Accurate’ charge mode). On the
other hand ‘equalizing’ is when we do it ‘manually’ as outlined below by fiddling around with the
individual cell tap connections or with a Balance Buddy, charging one cell at a time. Both wind up with the same net result..
both cells in the pack at full charge. * Q: At what point do you consider the 'balance' is bad? 10th of a Volt?
More? Less? My packs have cells that are never identical. Are they bad? * Several hundredths
of a volt either way is not an issue.. a few tenths of a volt is a problem. My rule of thumb has been if the cells are at
more than a 10th of a volt separation, I re-equalize or start a balance charge. Variation can creep in over time due
to the A123's unique molecular 'shag carpet' lattice of the plate material. Every cell will have small differences in plate
area right off the production line which gives rise to a slightly different rate of charge absorption and rate of discharge
so small voltage differences between cells are routine. Additionally, an over-discharge / under-volt occurance can introduce
slight resting voltage differences. Letting them go unattended (not checking and balancing or equalizing routinely) can
lead to trouble, but finding the cells in your pack not perfectly balanced at all times does not necessarily mean
you have a catastrophic problem. * Q: I've got an A123 pack that originally held balance just fine but now that it's been
in service awhile, it won't hold balance.. after a balance charge, a few days later I'm seeing the cells way out of balance
(more than a 1/10th of a volt) again. Is the pack ok? * The short answer is 'no; the pack is NOT okay'. This keeps cropping up.. there's
quite a few variations on the 'inability to hold balance theme'; common ground with all of them involving previously
known to be stable packs relate directly back to the use patterns of the guy in charge of the equipment. Lets
look again at the 'Achilles Heel' of A123. Over-discharge, or 'run flat' can and often does do damage to the cells. The
severity and length of time of the 'under-volt while under load' condition can impact the amount of degradation to the cells.
Regardless, the situation is not uncommon.. bumping a switch in handling, leaving the system 'on'. Working with the system
on the bench setting up servo throws and radio programming and the phone rings.. dinner is called... my kid stubs her toe,
somebody is at the door..whatever. The damage to the afflicted cell(s) can be inconsequential all the way up to
catastrophic.. a couple of examples: "My pack, after balance charging and showing the same voltage
for both cells will be out of balance by as much as 1/10th of a volt a few days later.. when I put the pack back in
balance charge mode it only takes 40ma and about 5 minutes to re-balance again". In this situation, the damage
to the cell was slight... the resting voltage of the 'afflicted' cell has been 'downgraded' a bit by the run flat
situation, and doing capacity checks of the individual cells in the pack would reveal no significant capacity loss.
On the other end of the spectrum for this type of failure is catastrophic damage to one or both cells.. and manifests
itself to the operator as a total breakdown of the cell.. the pack gets warm to hot on the charger and the afflicted cell
has almost no voltage at all (under 2v). Continuing to charge the pack can lead to heat distortion of the heat
shrink and end caps on the pack. * Folks, 'Run Flats' are not warrant-able failures... and known to be stable packs don't just develop
this chronic out-of-balance condition.. (cells can't overcharge or overdischarge or reverse polarity charge themselves). It's
invariably operator error or equipment failure.. switches that fail-safe to 'on', then unbeknown to the operator fail
or go intermittent or continuously draw a few milliamperes regardless of switch state are insidiously problematic. Despite
'smart switches' that ain't all that 'smart' along with other technological marvels that attract us because they
allegedly absolve us from using our own brains we still fall prey on occasion to the simple 'oops.. switch got left on
again' occurrences. The key to avoiding these failures is awareness and a healthy respect
for 'Murphy's Law'. Knowing that NOT insuring and verifying your system is really 'off' leads to grief with your packs
(not just A123's.. it's a form of Russian Roulette with every technology type) does if for most folks. However, Murphy
intrudes on occasion.. it's not a perfect world and after having cursed myself out a half dozen or so times over the last
25 years for being the 'operator in charge' and having failed to double-check & insure the system was in fact
still "off " and damaging my own packs in my own planes as a result hasn't changed
either the failure incidence rate or the feeling of abject stupidity for having bumped that switch while loading or unloading
the plane into the truck or unplugging that pack from a load before leaving the room or answering that call of nature....
which is why I advise recharging and checking the packs after the last flight of the day, then unplugging packs from switches
when you break the plane down for transport and never leaving a room with a radio system switched on. Now, if I could
just follow my own advise, I'd likely be a happier camper. * Q: Is there some way I can just rapid charge each cell; one at
a time, to get the pack back in range of the charger’s balancer? * A: Yep, it’s not overly difficult
really; you’ll just need to charge the cells independently (separately). Fortunately, and unlike Nicad or NiMh packs,
your A123 packs are likely already wired to allow access to each cell separately thru the three wire balance tap. The ‘usual’
way to gain access to the cells individually is to make up a couple of short aileron extensions with the contacts moved around
in the housings allowing you to access the cells one at a time. Use caution and a voltmeter to confirm polarity of the individual
cells. (on the back of our packs is a color code to tap info sticker) If you don’t want to fiddle around with contacts
and sweat polarity issues you can use a Balance Buddy. In either case, once you have access to the individual cell via your
jury rigged aileron extension or a Balance Buddy, just connect your A123 compatible charger and fully charge that cell. You
can use a charge rate as high as the connectors you are using can handle, however I just use the charger’s default 1C
rate (making sure the charger correctly identified it as a 1S single cell A123 battery) and when the charger completes topping
off that cell, I’ll check/charge the other cell to get it to full voltage too. (Remember to re-check for the change
in polarity on the other cell if using a modified aileron extension before starting a charge!!) * Q: So, what’s a “Balance Buddy”? * A: It’s a 2 cell A123 pack ‘Equalizer’
module that sits between your charger and the pack, plugged into the packs three wire lead.. Basically it’s just
a simple little 20 dollar switching gizmo we cobbled up to take the grief out of fussing with modified aileron extensions
to gain instant access to the individual cells via the Univ cell tap. You just plug it into the packs Univ cell tap connector
and then plug your A123 compatible charger into the Balance Buddy. There’s a three position switch.. Cell 1, Both and
Cell 2. Just pick which cell you’d like to charge, (1,2 or both) set the switch to that selection, and start the charger.
The Balance Buddy makes it fast and easy to quickly ‘equalize’ an out of balance pack with any
A123 compatible charger… with or without a balance feature!Used with an ESV, you can check and load each cell
individually, and check the packs total voltage. Used with a reversed (two male, 1 female) ‘Y’ harness and
a voltmeter, it turns a ‘dumb’ (no voltage display) type basic unbalanced A123 charger into a competent ‘check,
charge, equalize’ capable ‘smarter’ charger. Best of all, it means simple, fast, no hassle re-balancing
at the field without wasting any time waiting on a 100ma ‘balancer’ in a ‘smart’ charger to finish
it’s job. Click here for more info on the Balance Buddy * Q: These are Lithium’s.. don’t lithium’s need a Voltage Regulator for use as a
an Rx pack? * Once more for you folks out there with LiPoly
or LiIon systems.. no regulator is required for modern Rx’s and Servos with these A123 LiFe 2 cell packs... because
these packs at full charge and under load are operating at about 6.6v.. the same voltage level as a fully charged and loaded
5 cell 6v NiCad pack. If you have the latest generation 2.4 radio system and digital servo’s rated at 6v and your system
exhibits twitching or instability on an A123 2 cell pack then something is wrong with your Rx or Servos.I’ve
had folks with 5 cell Nicad packs complain about twitch and jitter with some recent Hitec servos.. these were replaced by
Hitec, problem solved. Folks, if your running some dinosaur Rx or antique servos, all bets are off; proceed assuming you’ll
be using 4 cell NiCad packs until you upgrade your radio gear. However, if your running antibody's 2.4 Rx system and modern
digital servos rated for 6v operation you’ll find the A123’s operate the system perfectly. Rule of
thumb, if your running 5 cell 6v Rx packs without regulators, your good to go with A123’s and no regulators. Note:
If you’re a Heli pilot with a gyro that won’t operate with a 6v Rx pack, then your outta luck too. * Q:
I’ve got a DA Engine.. can I use this as an Ignition pack? * Yup.. according
to DA there are no issues with LiFe packs with their ignition modules. Again, no regulator required. If you’ve got something
other than a DA engine with a different ignition module, you’ll need to check with that mfg or distributor; but again,
as a rule of thumb, if you’ve had no difficulties running a 5 cell NiCad or NiMH pack on your ignition without a regulator
then the A123’s should do just fine. Remember the loaded voltage of LiFe ignition pack is 6.6v.. the same as a fresh
NiCad 5 cell pack. * Q: How about use for Turbine ECU’s? * Since a
2 cell LiFe’s nominal operating voltage under load is @ 6.6v attempting to use them as a drop in replacement can (and
likely will) lead to flamer starts and lousy throttle controllability response. We've made available 3 and 4 cell liFe Turbine
packs for those folks that need higher voltage for the ECU, as always, check with the ECU/Turbine MFG or Distributor
for the required input voltage for their device. Please note that these 3 and 4 cell packs need Balance Charging support
and for those packs the only balance charge connector I have available is the FMA CellPro plug. If you already have a Cellpro
or Multi-4 charger, you will be good to go with a NoBS A123 ECU pack. * Q: I read somewhere that A123 LiFe cells can be charged at up to 10 amps.. does that
make sense? * Yup.. that’s correct. According to A123’s
specs.. 10 amps. Of course, here’s where a brain on the part of the end user comes into play. What are your connectors
and switches rated for? If your like me and use HD system switches and industry standard battery and servo connections, then
you’d better cut the charge rate down to what those connectors can handle.. 3-4 amps. Tops. If your using direct connections
from the pack to the charger via 18g wire and Deans or Anderson connectors, then you can use the 10a charge rate if your charger
will go that high. For most of us, the 3 amp rate through the HD switch ports makes sense, and the difference in time (15
min vs 3 minutes for a normal battery refueling at ½ discharge) is of no consequence. * Q:
I've got a 25% Sized Yak with a DA 50, all digitals and I fly the pants off it.. what A123 LiFe setup would you recommend? * Keeping things light is always important.. and in the 25% birds, battery system weights have a bigger percentage of
total weight impact than in the larger birds. In your situation a minimum setup would be a single 2300 A123 LiFe pack
with dual leads and feeding dual switches. For the Ignition, a single 1100 A123 LiFe pack and with this setup, you'll likely
get 3-4 flat out flights between charges at least.. maybe more. See the notes above about how to find out how many flights
you can get with your bird the way you fly it. * Q: I’m Running two 2400
Nicad 5 cell packs with dual switches in my 40% Extra.. DA-150 up front. What will I need to upgrade to A123’s? * An A123 Charger, a charger cable to connect to your pack or switch, a balancer cable, a servo extension to
make your balancer cable out of and a pair of A123 two cell 6.6v 2300 packs. You MIGHT want to pick up a pair of 'ernst'
type charge ports for the side of the plane to use the balancer for on-board charging if you don't have the FMA Cellpro or
Multi-4 charger.. Note that your CG may change.. this dual pack A123 system will weigh approximately HALF of what the two
5 cell pack NiCad system weighed. For the ignition.. one more as above.. it'll probably run the engine all day. * Q:
Same Question, same size bird, but I have a single 4500 NiMH 5 cell pack with dual leads & switches and
I don't want to lose flying time with the 2300 LiFe's. * Same answer as above.. use a Dual 2300 LiFe pack
setup with your two switches. You won't lose a bit of flying time.. in fact, you'll probably gain a flight or two and will
have improved the dependability a bit to boot without adding a bit of weight. * Q:
I have an 'IBEC'.. an ignition battery eliminator. Lets me run the ignition off the Rx pack. Do I need any special cabling
on an A123 pack to make this work? * A:
Over the past 30 years I've seen several 'ignition battery eliminator' setups come and go... they are usually a small module
that sits between the switch and the Rx and port power to the ignition module. They don't normally require any extra connectors
on the pack. Some have voltage step-downs to regulate power to an acceptable range for various ignition types. I haven't seen
any of them that has cabling on them as large as our switches or packs.. and to work, the IBEC has to pass power to your
Rx through their circuit board, cabling & connectors... another set of potential failure points. - I won't use one and I don't recommend them. One of the more common failures
on larger gas powered models is ignition modules.. when the module shorts out from vibration and heat the ignition battery
pack goes dead a few moments later.. leaving the pilot with an engine out 'dead stick' landing. With an ignition battery eliminator, if
the module shorts, more often than not the pilot is left without power for the Rx too. That's not a dead stick landing. That's
a dead aircraft arrival, not a recoverable situation. In all commercial
RPV's, military drones, etc, the telemetry system has its own power supply, as does the engine ignition system and the crafts
Rx/Servo system. Separation and redundancy.. in larger models, much preferred over combining systems on one pack. - For the most part, folks that
pursue the ignition battery eliminator attempt to justify it as a weight issue.. reality proves that concept as wrong-headed...
lets look a small 30cc powered 12 pound bird. 12 pounds x 16 ounces to the pound = 192 ounces. The plane likely carries
20-28 ounces of fuel. An 1100ma 123 pack weighs 3 ounces. The three ounces won't have any material impact on the performance
of the airplane.. however saving those three ounces could easily cost you the entire investment. Of course if your determined
to save the three ounces.. you could put a tad less fuel in the tank when you fill up. * Q:
Do I have to buy a new charger to charge A123 packs? * Yes.. Normally.
Unless your charger is A123 compatible. There’s a work-around available called the ‘dapter’ to allow safe
charging of A123 cells with a NiCad/NiMH charger.. do a quick internet search for this device to see if it fits your needs
and will work with your current charger. The feature that I like to see most on a charger used for A123 support is the balance
feature.. while there’s likely to be ongoing debate on the 'need' for balancing A123’s with every charge there
is absolutely no doubt that 99% of the issues experienced to date with A123's would have been avoided
outright had the user employed a quality balance charger and checked individual cell voltages on every charge routine. * Q:
Do I need to disconnect the switches from the Rx if charging two packs at the same time like I did with my NiCads and
NiMH parallel setups? * Ahh... the insidious 'common ground issue'. Yup; chances are; unless your
charging through a power box designed to eliminate this issue, then you'll need to unplug one of the switches to eliminate
the common ground. * Q: Do I need to Formation Charge A123 LiFe packs? * According
to A123, nope. However, prudence dictates that establishing a capacity number and verifying the pack is stable before putting
it in service is good practice with any battery technology. Bear in mind that in a charging/cycling situation and with
these cells the concept of ‘slow’ charge' and ‘fast charge’ and 'formation charging' no longer have
the meaning we associate with NiMH and NiCads. The normal check routine for A123 would be to charge WITH the balancer
feature in use and the charge rate should be 2 to 3 amps. Use a discharge current of 1 amp, and a discharge cutoff voltage
value of 2.5v per cell. Bear in mind that with these settings pack capacity reporting with your cycler will be somewhat less
than the MFG's rating since we have adjusted the discharge cutoff up a bit to provide a safety margin for the cyclers discharge
cutoff trigger. Since A123's do not benefit from forming or 'cycling' in the traditional sense, there's no need for repetitive
cycles. I run the check cycle once on a new pack and again, once at the start of a new flying season or any time I note
a change in pack performance. * Q: My Charger can charge A123 and has a cycler, but when I set a 2v per cell cutoff, at the end of
the discharge one cell is way below 2 volts! What's up with that? * We've seen
this in the Hitec X4, it's also common across several other multichemistry charger/cyclers. Whats happening is the cyclers
discharge cutoff trigger is watching the total pack voltage and ignoring the individual cell voltage. This is a source
programming error in my opinion, just as the charge routine is individual cell voltage controlled, it's no less important
for lithium packs to terminate the discharge routine based on individual cell voltage. Here's the 'issue': A123's have a very,very
sharp 'knee' in the discharge curve and actual capacity varies as much as 5-10% between cells. (an artifact of A123's
'nano' plating technology.. negative plate surface area varies a bit from cell to cell) This issue can set up an overdischarge
condition on the lower capacity cell, so we've adjusted the discharge target up from 2v per cell to 2.5v per
cell to give a cycler that does not have individual terminal voltage control a bit of 'padding'
as a safety margin. * Q: I have a standard A123 Charger
that won’t ‘cycle’ or discharge. Can I use my programmable NiCad/NiMH charger/cycler (Triton, Triton II,
Multiplex LN5014, Accucycle Elite, etc) to discharge them and get capacity numbers for evaluation and testing? * Yes.. IF you can set the voltage cutoff on discharge and discharge load, no problem. (most cyclers
are programmable for low voltage cutoff in the Nicad or NiMH menu's) Again.. this is for cycling for formation or evaluation..
not for charging. The discharge rate should be no more than 1amp, the voltage
cutoff should be 2.5v per cell. (was originally 2v, recently updated, see question above) See your charger/cyclers manual
for how to effect these changes and use only an A123 LiFe Compatible Charger/Charge Routine cabled correctly to balance
charge A123 LiFe packs. * Q: What Charger do you recommend? * Lordy..
well; there's an awful lot of chargers out there that'll handle LiFe now.. FMA's Cellpro and Multi-4 are my personal on the
field favorites since they accommodate balance charging with just one three wire connection to the pack and with a simple
adapter can balance charge, check individual cell voltages and produce a reliable reading on the percentage of charge
in the pack right through the switch chargeport. (switch mod may be required, see
the setup guide!) Hitec's X4 is an excellent multi-port charger at it's price-point that has a cycler in it and it's easily
upgraded to single cable charging with our available adapter. Since it's quite a bit larger than the FMA Multi-4, I
prefer it for 'bench work'. You'll find there's a fair number of charger reviews on the modeling discussion websites with
plenty of opinions out there.. in my experience, if a pack can be easily checked and balance charged via the switch chargeport,
the chance of a pack or charger issue ruining your day are reduced by a potentially dramatic degree. See our Setup Guide for charger and cabling discussions and various setup solutions. *
Q: What Field Charge rate do you use? * I normally field charge at 3 amps.. but that’s the limit of my switches and connectors. When I field charge with
the balancer on the first charge of the day, it’s at 2 amps. How you set up and charge is really limited by the connectors
and wiring and the charger capabilities. If you feel the 'need' to charge at higher rates, one work-around to speed up charge
time with chargers that can work at higher rates is to charge the pack directly.. not through the standard system connectors
on most chargeport switches. Install an Anderson or Deans connector on the switch input side, order the pack with Anderson
or Deans plugs to match and disconnect the pack from the switch and charge through the pack feed. * Q:
My NiMH packs are often pretty low after just a couple of days of sitting. Will these (LiFe) hold their charge better? * Yup. Lots better. And better than NiCad’s, too. The rapid
self discharge characteristic present in low impedance Nicads and NiMH cells is just not present with LiFe cells. BUT.. (there’s
always a ‘but’.. you notice?) we are in a brave new world or radio gear and systems applications. In an awful
lot of equipment out there I’m finding system loading present at the pack even with the system ‘off’. On
some of the 2.4 systems and most ECU’s and some ignition modules there’s a constant current draw of 2-4 milliamps..
so, leaving packs plugged into the switches for weeks or months at a time can cause grief and surprises. I don’t like
grief and surprises. I unplug my packs from the switches when I’m done flying. I strongly recommend you do the same.
Get in the habit, just do it. * Q: How should I store A123 packs? * My preferred method is to balance charge and cycle, record the capacity info, then balance charge again and disconnect
them from all devices. What these cells DON’T like is discharge to 0 volts under a load and they don’t like sub
zero weather conditions. Since they have a very low self discharge characteristic there’s no risk of finding a zero
voltage pack in the spring after a winter layup. If you keep your plane in an unheated environment and suffer with sub-zero
conditions where the plane is, it would be prudent to take the packs out of the plane and bring them in where you are. Like
most batteries, they like the same temperatures you like. * Q: What happens when the plane
gets hot? My NiMH packs suffer on hot days, I notice lower voltage and capacity. Same when it’s real cold out. * Another thing I like about the LiFe’s is the thermal increase performance… these cells are more resilient
than any other battery type to temp build-up inside the application it’s powering. A123’s specs indicate routine
operating temps as high as 140 degrees with only a 12% drop in capacity. So, if your big bird has a lot of canopy glass cooking
your NiMH packs down quickly, LiFe will be a pleasant improvement for you. On the other end of the scale, once the outside
temps drop to 4 degrees below zero F we see about 20% loss of capacity. Just in case you like to fly in Alaska in the winter,
take a flight or two less than in the summer. * Q:
What happened to A123 Racing? According to their website A123 Racing is no more? * A123
Systems officially discontinued all A123 'Racing' products back in January 2011... they don't market directly to or in the
R/C hobby anymore and they have discontinued retail oriented 'A123 Racing' branded pack assembly and products. Frankly, the
finished pack product they made available to R/C customers was not assembled to anywhere near the same standards American
assemblers demanded for their customers. Simply put, US shops like ours declined to purchase their 'finished' product and
built a better pack with their raw cells, properly cabled and reinforced for our R/C flying, RPV and Robotics applications
than they could. A123 Systems is still very much in business, and we are still buying cells from them. A123 Systems is quite
'healthy', has no plans to discontinue either of the cells we use in the R/C hobby as those same cells are also exceptionally
successful within the portable tools market. * Q: Can I get custom electric flight packs from you built
out of A123’s? * Not without using
a gun. I worked for a guy that was a pretty smart feller once.. he used to love to say ‘Just because you can do something,
doesn’t mean you should’. Over the course of the last 20 years I’ve had a lot of folks tell me ‘I’m
missing the boat’ with electrics and electric flight. Gent’s, I built that boat… back when we
used to tear down Drill Motors for gearboxes and measure current draw by the amount of smoke coming out the back on the climb
out. I have a wall full of trophies and fond memories of the days when ingenuity in electric powered modeling and pilot skill
made a bigger difference than the amount of money thrown at the challenge. - My current joy in the hobby is The Big Birds..
it’s what I fly when I finally get out to enjoy a day as a modeler. This is my retirement, and what I do is a labor
of love.. not a driving grind to rake in the bucks and fleece folks. So, there's no big shop, no leveraged inventory, no staff
to supervise, no national ad campaigns, no smoke and mirrors and 'man behind the curtain' crap. It’s just
me and my many decades of experience in this narrow field, and that’s the way I like it. Since I'm still working
despite the crushed economy, I guess it's how my customers like it too. The amount of work that comes in here from the commercial/military
RPV end and the folks flying Giant Scale and IMAC keep me more than busy enough to pay the bills; they are, by the nature
of what they are doing and the level of investment in time, effort and craftsmanship they do it with; competent
modelers and pilots... and they keep food on the table without driving me batty with ‘is the red wire important’
questions. So, no.. I’ll not be building packs for the electric flight folks in our fine hobby any time soon. Don’t
ask, and I promise not to promptly skin you alive and feed the cat with your entrails. J s Steve Anthony NoBS Batteries
/ Hangtimes Hobbies October 2008, updated April 2012 email: hangtime@hangtimes.com
*A123 & Nanophosphate
are trademarks of A123 Systems, Inc. All A123 cells and chargers assembled and distributed by Hangtimes Hobbies and NoBS Batteries
are acquired from A123's sole licensed US Distributor. All rights to A123 technology and trademarks reserved by A123 Systems
Inc
|
 |
|
Hangtimes Hobbies NoBS Batteries
|
|
|
 |